More Technical Details about Fully Automatic Pipe Bending Machine: Unraveling the Mechanics of Precision and Efficiency
The manufacturing world is constantly seeking ways to optimize production processes, and the advent of the fully automatic pipe bending machine marks a significant leap towards achieving this goal.
Beyond Basic Bending: Understanding the Core Components
A fully automatic pipe bending machine is more than just a mechanical arm.
1. Feeding Mechanism: The journey begins with the feeding mechanism, which accurately transports the pipe into the bending die.
- Roller Feed Systems: These systems utilize powered rollers to push the pipe forward, ensuring a smooth and controlled movement.
- Clamp Feed Systems: Clamp feed systems grip the pipe securely and advance it incrementally, providing greater precision for complex bending geometries.
- Push Feed Systems: Hydraulically powered push systems offer robust performance and are ideal for bending heavier pipes.
2. Bending Die and Mandrel: The heart of the machine lies in the bending die and mandrel. The die, typically made from hardened steel, provides the contoured surface against which the pipe is bent. The mandrel, a specialized tool inserted into the pipe, prevents wrinkles and collapses during the bending process. The selection of the appropriate die and mandrel depends on the desired bend radius, pipe diameter, and material properties.
3. Clamping System: To ensure a clean and precise bend, the pipe must be securely held in place during the bending operation. This is achieved through a powerful clamping system, which can be:
- Hydraulic Clamping: Hydraulic cylinders provide consistent and adjustable clamping pressure, accommodating a wide range of pipe sizes and materials.
- Pneumatic Clamping: Pneumatic systems offer faster clamping cycles and are often preferred for high-volume production.
- Mechanical Clamping: Mechanical clamping systems are simpler and more cost-effective, but may offer less flexibility in terms of clamping force.
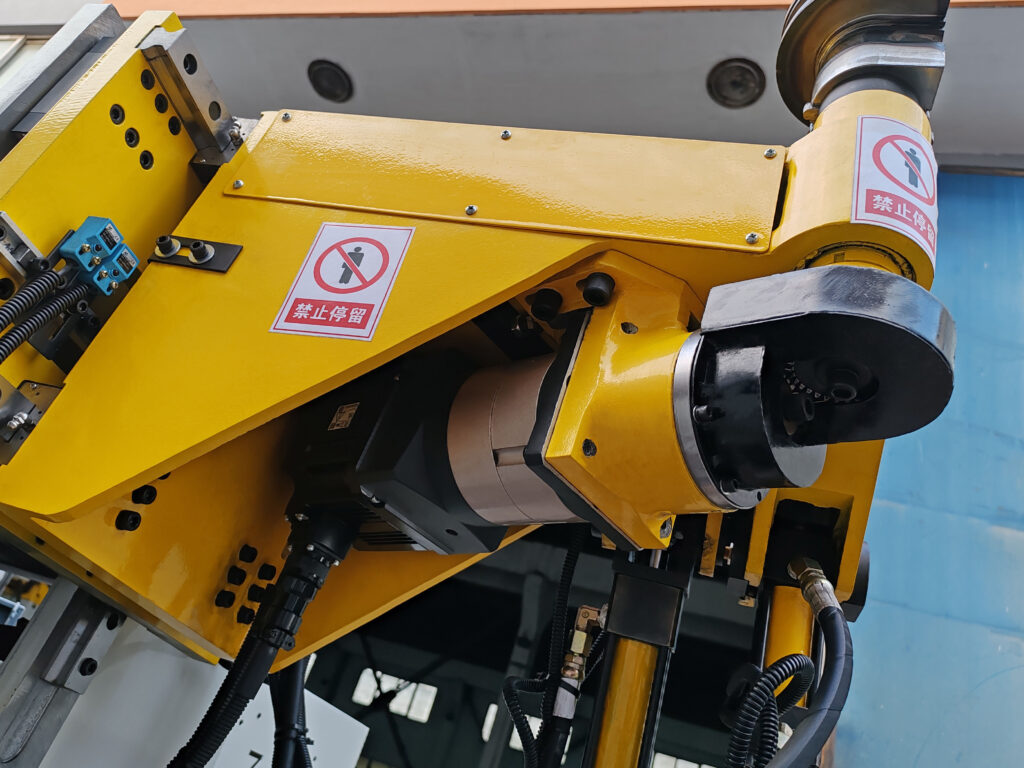
Advanced Features: Pushing the Boundaries of Bending Technology
Beyond the core components, many fully automatic pipe bending machines offer advanced features that further enhance their capabilities and versatility:
- Multi-Stack Bending: This feature allows the machine to bend multiple pipes simultaneously, significantly increasing productivity.
- Boost Bending: Boost bending technology utilizes internal pressure to assist in the bending process, enabling the bending of thicker pipes and tighter radii.
- 3D Bending: Advanced 3D bending capabilities allow for the creation of complex, three-dimensional shapes, opening up new possibilities for design and fabrication.
- Data Logging and Traceability: Integrated data logging systems track bending parameters and provide valuable insights into the production process, enabling quality control and process optimization.
The Benefits of Automation: A Paradigm Shift in Pipe Bending
The adoption of fully automatic pipe bending machines offers a multitude of benefits over traditional manual bending methods:
- Increased Productivity: Automation significantly reduces cycle times and increases output, leading to substantial productivity gains.
- Improved Accuracy and Consistency: Precise control over bending parameters ensures consistent results, eliminating variations and reducing scrap rates.
- Enhanced Safety: Automation removes the need for manual handling of heavy pipes, reducing the risk of workplace injuries.
- Reduced Labor Costs: Automation reduces the reliance on skilled labor, leading to significant cost savings.
- Greater Flexibility: The ability to program complex bending sequences and easily switch between different pipe sizes and materials provides greater flexibility in production.
Fully automatic pipe bending machines represent a significant advancement in manufacturing technology, offering a powerful combination of precision, efficiency, and versatility. By understanding the technical details of these machines, manufacturers can make informed decisions about their implementation and unlock the full potential of automated pipe bending.